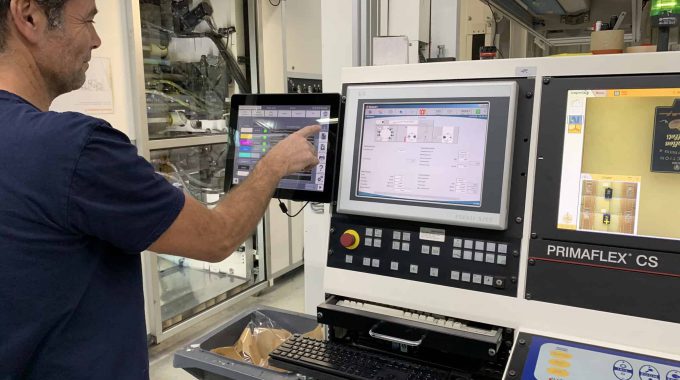
柔版印刷中的粘度标准化
控制柔版和凹版印刷中最大变量的新方法
介绍
在我们公司的历史上,我们应用过各种类型的粘度传感器:旋转式、落球式、落活塞式和声波式。 这些传感器之间的相似之处在于它们都是用杯子校准的,在我们的例子中是带有 4 毫米出口的 DIN 杯子。 这本身效果很好,并且由于缺乏更好的替代品,DIN cup 4 成为柔印和凹印行业的标准测量。 2017年XNUMX月,在寻找更好的解决方案时,我接触到了 Rheonics SRV 作为我们一直使用的传感器的替代品,这些传感器太不准确且可重复性不足。 2018 年 2018 月,我们开始测试其中两个传感器,8 年 XNUMX 月,我们为 CI 印刷机的所有 XNUMX 个印刷站配备了 Rheonics SRV。 去年我们进行了多次测试,积累了经验和新的见解。 我们开发了一个公式,将 SRV 提供的单位厘泊 (mPaS) 转换为 DIN Cup 4 秒,因为我们习惯使用这些单位。 几个月后,我们决定完全停止使用 DIN Cup 装置,原因将在本文中阐明。
当前的印刷机在调整方面非常精确(在μm范围内),并且具有很高的自动化程度,例如100%检查系统,网纹辊和印版滚筒的全自动压印设置,自动套准控制以及在线光谱颜色测量。 但是,在打印过程中最大的变量,即油墨的粘度,仍使用手动确定的单位进行测量! 在许多情况下,甚至自动粘度控制也可以通过杯进行校准,因为操作员习惯于在杯秒内思考。 在实践中,通常不进行粘度校准,因为这很耗时,或者因为杯子很脏或无法使用。
粘度是印刷品最终质量中非常重要的参数。 如果粘度不正确,则流动特性和墨水层厚度将发生变化,这将导致打印质量问题。 另外,油墨粘度调节不当会导致油墨消耗过多。
准确性
每个操作员都习惯于使用某种粘度测量杯。 这些测量从未完全标准化,仅在相对较窄的测量范围内“可靠”,且误差范围较大(5-10%)。 这些错误中的一些是杯本身引起的,其他是操作员技能的函数。 测量不可重复。 对粘度有很大影响的温度难以控制。 杯子的污染和不同浓度的墨水会影响跳动速度。 所有这些加重了DIN杯测量的可重复性和准确性。
实际上,误差范围可以高达5-10%,这是很大的粘度带宽。 例如,对于粘度为20 s的墨水,误差范围在5-10%之间意味着带宽在1 s和2 s之间!
其准确度和重复性如何 Rheonics SRV 与 DIN 杯测量比较?
这是摘录自 Rheonics SRV规格表:
粘度范围 | 0.4至250,000 + cP |
粘度精度 | 读数的5%(标准) 1%及更高的精度 |
再生性 | 胜过阅读的1% |
温度 | Pt1000(DIN EN 60751) |
工艺流体温度 | -40,最高300°C(575°F) |
环境温度 | -40至150°C |
压力范围 | 最高7,500 psi(500条形) |
传感器的操作基于浸入流体中的振动元件,其共振会受到流体粘度的抑制。 这 Rheonics SRV 与其他振动传感器的不同之处在于,它的谐振器是完全平衡的,因此其精度不受机械环境的影响。 它也非常坚固,这意味着必要时可以用浸有溶剂的抹布擦拭来清洁它。
制造商的规格表明它具有宽广的测量范围和很高的精度,但是实际上这意味着什么呢? 我们通过将20 g溶剂添加到25 kg墨水中来测试其准确性。 传感器记录到的粘度变化为0.1 mPaS,这相当于02秒的杯子测量差! 这是该行业中以前未知的粘度测量精度。 而且由于SRV将精确的温度测量值整合到传感元件中,因此有可能准确补偿温度的影响,这将在下一部分中进行介绍。
我们发现,使用杯子不仅过时,而且实际上适得其反。 几个月后,我们完全停止了转换为杯秒,最终将粘度的测量(印刷中的最后一个关键变量)提高到了与其余过程相同的技术水平。 我们终于到达了21st世纪。
非牛顿性,触变性和温度补偿粘度
由于测量的准确性和重复性 Rheonics SRV 传感器,我们对墨水的行为有了很多了解——有时比我们预期的还要多。 墨水是一种流变学复杂的介质,SRV 使我们能够深入了解 DIN 杯无法观察到的复杂性。
溶剂型油墨表现出非牛顿行为。 在剪切力的影响下,它们的粘度发生变化。 墨水还具有触变性,静止墨水的粘度与运动墨水的粘度明显不同。 固定墨水的粘度与移动墨水的粘度相差高达 20%! 此外,油墨粘度与温度密切相关。 在没有调节油墨温度的印刷机上,油墨温度以及粘度可能会因环境温度的变化以及印刷机本身产生的热量而发生很大变化。 我们首先探索的事情之一 Rheonics SRV 是墨水粘度的温度依赖性。
我们建立了一个测试设备,其中包括一个封闭的流动回路,在该回路中,墨水以与印刷机中墨水回路相当的速度连续泵入回路中,然后缓慢加热。 每秒测量一次温度和粘度,在一个典型的测试运行中会给出一千多个测量点。
图1中的图表显示了在20°C的温度范围内,多种不同墨水(改性的硝酸纤维素墨水黄色,品红色,银和聚氨酯白色)的粘度的温度依赖性。 在此范围内,粘度相差最多60%。
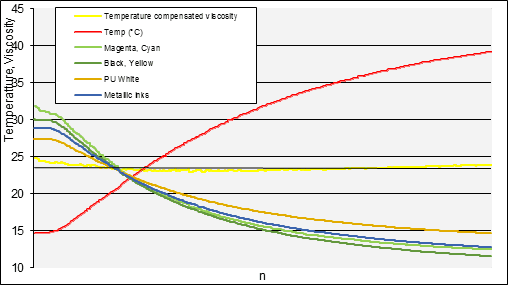
图1。 油墨粘度的温度依赖性
粘度测量的最重要用途之一是确定何时必须稀释多少墨水,以补偿打印过程中溶剂的损失。 溶剂蒸发会增加墨水的颜料含量,从而导致打印质量差和墨水消耗过多。 溶剂的这种损失也增加了油墨的粘度。 但是,由于粘度也是温度的强函数,因此有必要在温度和蒸发的影响之间进行区分,以确定溶剂添加的量和时间。
如果没有温度补偿,则低温下的墨水会给出较高的粘度读数,表明必须进行稀释。 但是,稀释油墨将产生较低的色密度,因为较高的粘度是由于较低的温度而不是较高的颜料负载所致。
使用图1中的图,我们开发了一种算法,该算法使我们能够补偿温度对粘度的影响,从而产生“温度补偿粘度”,这是颜料加载量的真实度量。 因此,它可以直接控制溶剂的添加以弥补蒸发,因为它将温度作为影响测量的变量来消除。
使用我们的补偿算法,我们可以将整个温度范围内的误差偏差降低到1%。 在自动粘度控制中,可以为每种墨水选择温度补偿。 我们已经为几乎所有使用的墨水确定了该曲线,并使用特殊算法确定了温度补偿参数,从而使我们最终可以实现对颜料填充量及其对打印质量的影响的更严格控制。
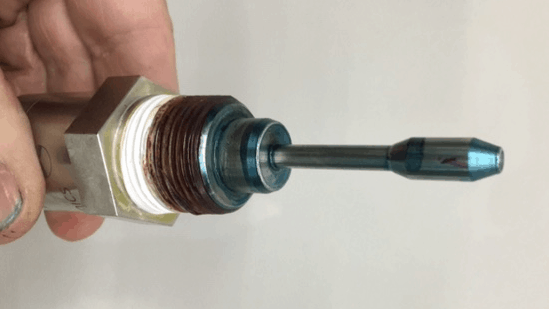
图2。 用青色墨水测量后的SRV传感器
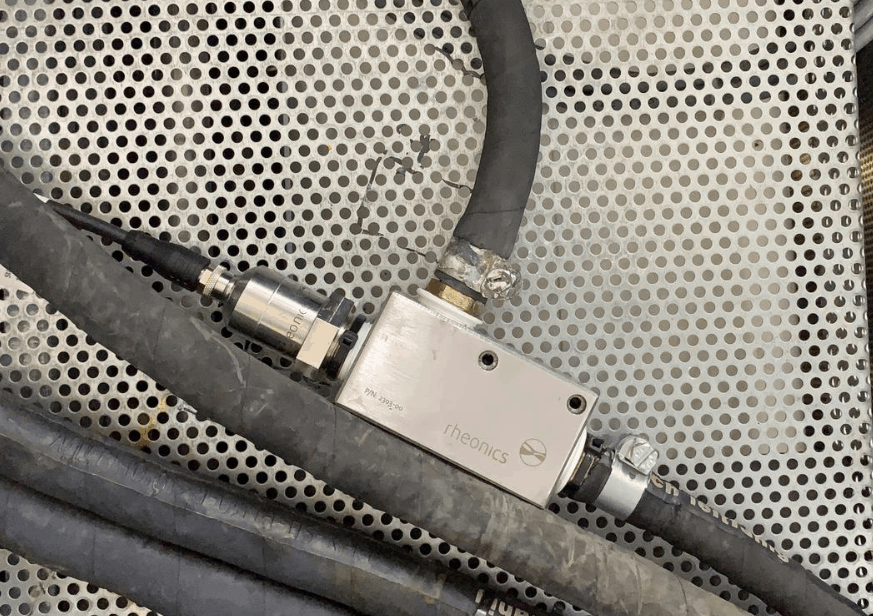
图 3. 安装在墨水管路中的 SRV,显示 Rheonics 打印适配器
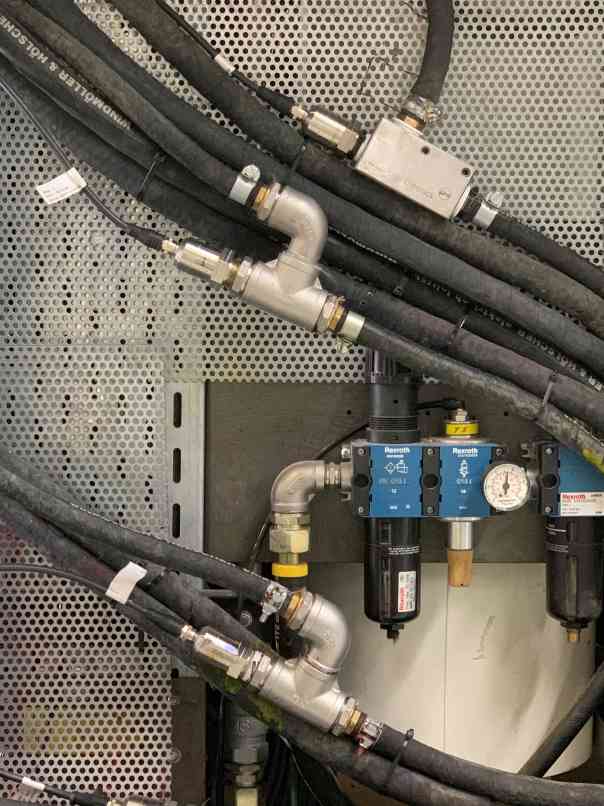
图4。 使用简单的三通作为适配器,在压力机上安装了四个SRV
装置
传感器安装在带有入口和出口的连接器中,并安装在墨水泵和刮墨室之间的供应管线中。 诸如机器振动或隔膜泵产生的压力脉动之类的影响不会影响传感器的运行或测量精度。
该传感器是免维护的–管路和刮刀腔室的每个清洁周期都可以确保再次清洁传感器,因为它会自动用溶剂清洗。 如图2所示,传感器上可能仅保留非常薄的颜色雾度,这对其精度或可重复性没有影响。 并且由于传感器的坚固结构,可以用浸有溶剂的抹布进行任何必要的清洁,而没有损坏传感器或更改其校准的危险。
所有传感器均通过工业级电缆单独连接至其电子单元,并与工业级 PC 进行通信。 计算机控制阀岛,阀岛又控制用于计量溶剂的气动阀。 该系统包括位于操作员控制面板旁边的触摸屏,可操作直观的用户界面 Rheonics 粘度控制软件 Inksight。 在创建用户界面时,显然必须清晰、直观、有效且操作快速。 界面显示一个仪表板,操作员可以在其中监控所有站的粘度。 触摸感应控件使操作员能够打开或关闭各个工作站、启用自动控制以及设置粘度限制。 一个单独的站集线器切换到一个显示器,用于监测粘度随时间的变化,并允许调整特定的传感器和阀门。
此外,当粘度变化太大时,该软件会通知操作员,并通过进行正确的纠正来解决问题。
自动控制,CS控制
在打印过程中,溶剂会不断蒸发。 随着打印速度的增加和墨水温度的升高,蒸发量增加。 SRV传感器每秒测量一次粘度和墨水温度的实际值,从而使软件能够计算温度补偿后的粘度。 这进而使控制器能够确定温度补偿的粘度是否落在期望的公差内。 控制器将根据与设定值的偏差量添加一定量的溶剂。 在打印过程中,与设定值的偏差仅可保持0.5%。 使用特殊的定量阀,可以添加实现这种精细控制所需的非常少量的溶剂。 下面的图是相同颜色的比例尺,垂直的品红色线表示自动加液。
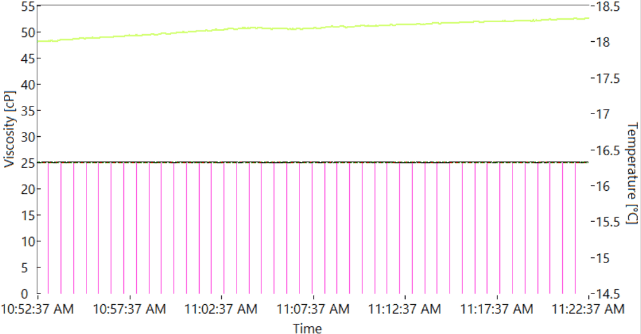
图5a。 温度补偿粘度和温度与时间的关系,垂直刻度粗
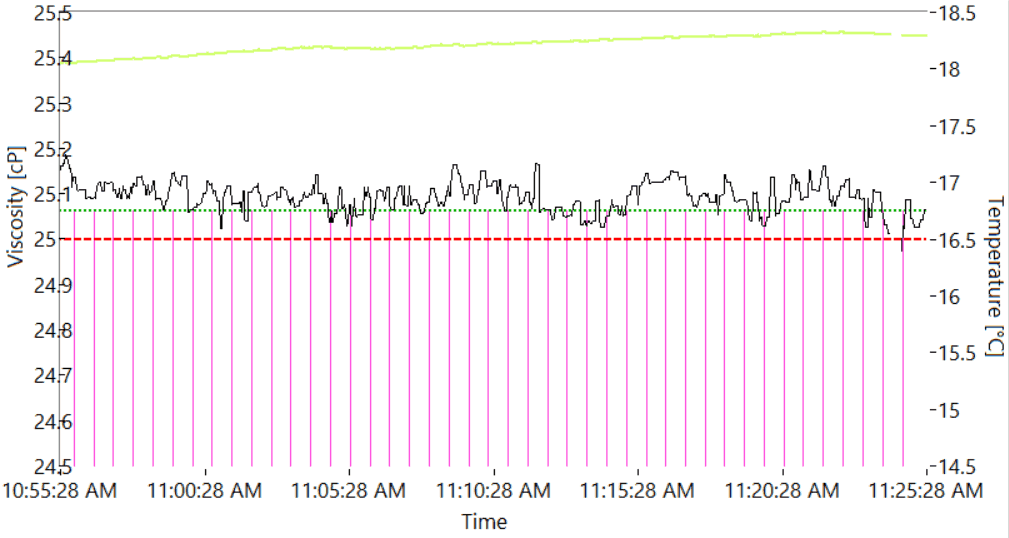
图6b。 与上述相同的图,具有扩大的垂直比例。 温度补偿粘度变化小于0.2 mPaS
基于SRV的控制系统非常精确,因为它可以快速补偿并经常补偿打印过程中不断发生的蒸发。 为了实现与设定值的很小偏差,有时系统每三十秒就会给10 g溶剂加药。
如果将粘度过高的墨水添加到墨水桶中,则控制将通过测量每个溶剂剂量下的响应立即做出响应,并相应地调整随后的溶剂剂量。 最后,以极小的过冲非常缓慢地达到设定点。 除了极其精确的控制外,当墨水桶中的墨水液位很低时,还可以保持粘度稳定,足以将墨水泵入系统。
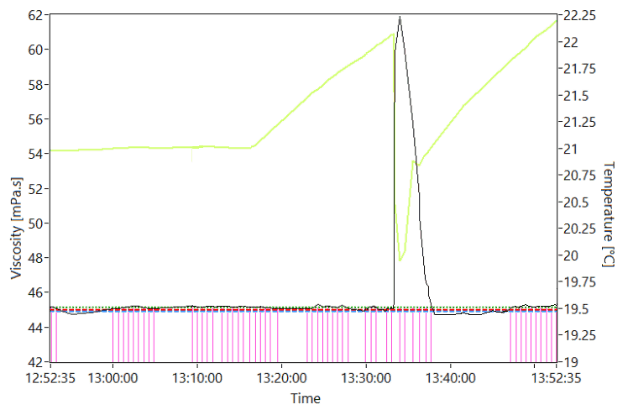
图6。 系统对在21度下运行的系统中添加大量冷墨水的响应。 C.注意温度补偿粘度的快速恢复时间。
质量保证,改进和标准化
经验丰富的操作员知道在使用的特定过程中对于哪种类型的墨水必须保持何种粘度。 这取决于墨水的种类-Pantone颜色以及特殊的挑战,例如金属和白色墨水所提出的挑战,它们在温度下的行为与“正常”墨水有所不同。 并且所需的粘度还取决于在其上进行印刷的基材的类型。
为了更好地理解问题及其解决方案,我们对墨水稀释对打印质量和测量的墨水粘度的影响进行了一系列实验。 根据这些结果,我们现在必须保持基材类型(纸,聚酯,聚乙烯,聚丙烯)的粘度。
在第一个实验中,将10 kg油墨稀释10%,按200米/分钟的速度运行,标记聚酯薄膜,并停止压力机。 用另外的3%的溶剂稀释油墨,使油墨循环直至粘度稳定,并且该过程总共重复15次。 除去膜,并用分光光度计测量所有15片段,并制作膜片段的照片以进行主观视觉评估。
下图显示了一系列稀释后的印刷质量的视觉外观。
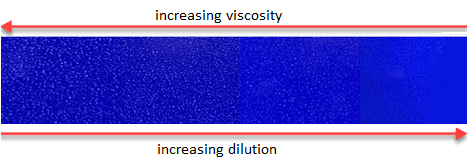
图7。 颜色浓度随墨水稀释度和粘度而变化
在最低稀释度(最高粘度)时,会沉积过多的墨水并且无法正常流动。 出现针孔,整体质量较差。 尽管针孔之间的颜色相当浓密,但由于针孔的高反射率,测得的密度较低。 随着稀释度的增加,粘度降低,流动性提高,但颜料含量减少,颜色变浅。 使用分光光度计测量每个样品并与数字 PMS 参考进行比较。 以下chart 和表显示 dE2000 和颜色密度作为稀释度和粘度的函数。 粘度差值参考样品6,即目标密度。
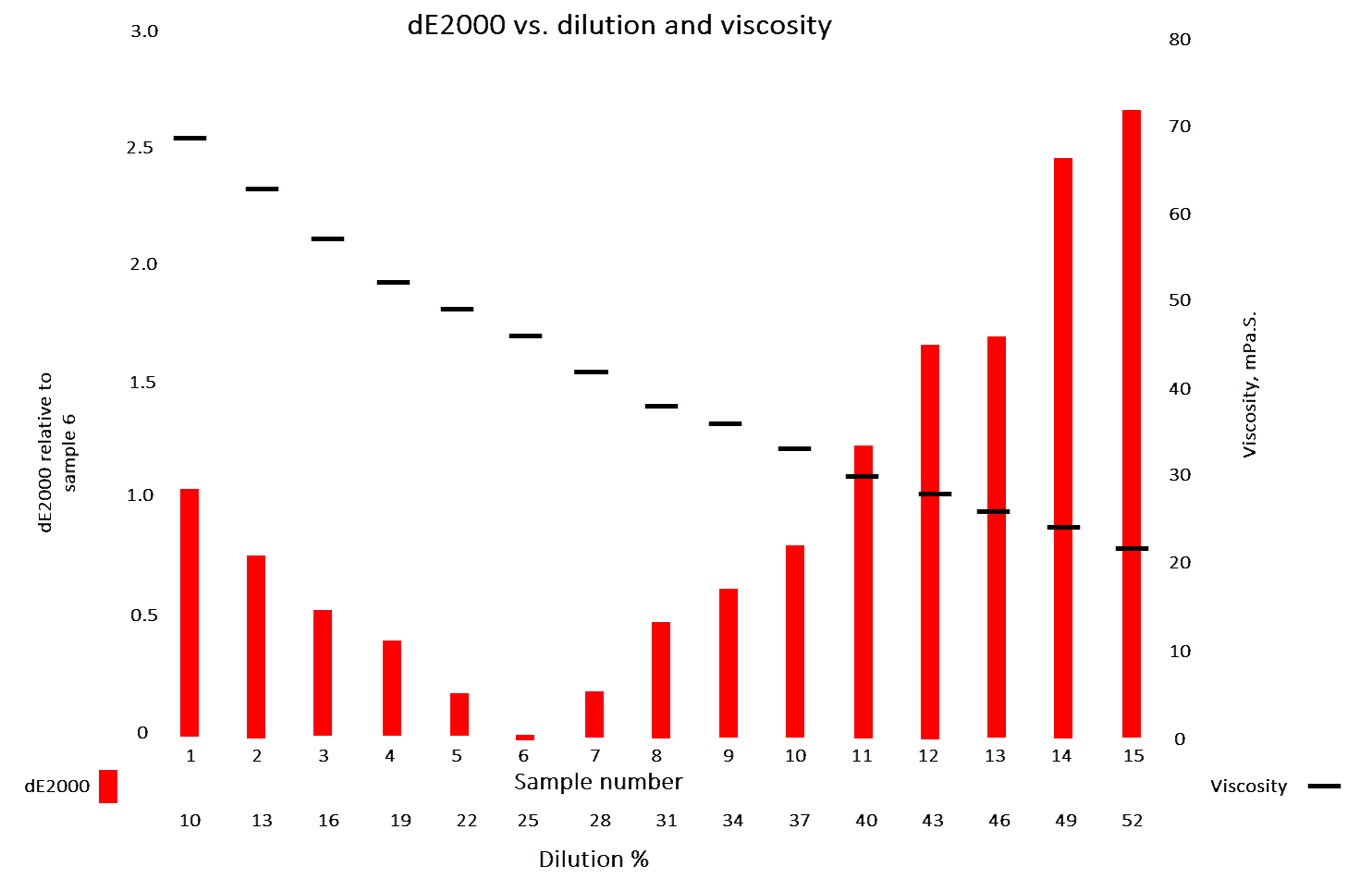
图8。 颜色密度是墨水稀释度和密度的函数。 dE2000值参考样本6
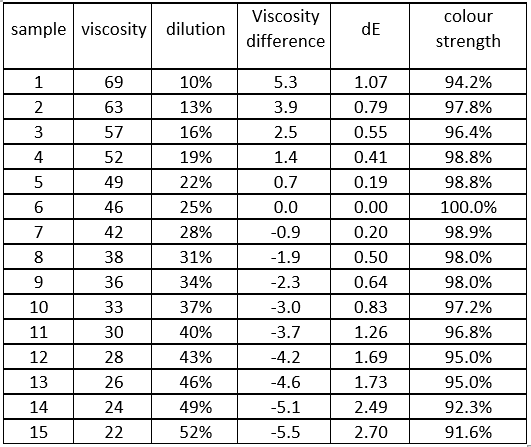
表格1。 dE2000和色强度与稀释度的数值。 粘度差相对于样品6
该实验表明,随着 Rheonics 系统可以实现非常精确的粘度控制,粘度带宽为0.5%。 通过大约每 30 秒添加极少量的溶剂,该系统可以实现 dE 值的极小变化。
在完成这些实验时,通常的粘度带宽为±0.5杯秒(约±2.2 mPaS),每5-10分钟检查一次粘度。 然后加入的溶剂量在0.2到0.5 kg之间(取决于墨水覆盖率,溶剂类型,网纹辊体积,机器速度和温度。
我们现在已经改变了印刷彩通颜色的过程,因为我们不仅知道必须针对基材类型保持哪些粘度,而且可以保持该粘度的严格公差。 某些基材需要较高的粘度,因为油墨“下沉”太远,结构变得可见,导致颜色强度下降,而其他基材由于其光滑的表面和良好的油墨接受性,需要较低的粘度。 凭借获得的经验 Rheonics 传感器,我们确切地知道对于基材类型(聚乙烯、聚丙烯、聚酰胺、聚酯、纸张和可生物降解)应保持哪种粘度,并且实际上已经为我们自己确定了标准化。
在第一次打印时,将测量Pantone颜色的颜色密度,然后操作员检查墨水对于相关基材是否具有正确的粘度。 (由于基材的表面质量可能略有不同,因此通常无法提前将油墨调到正确的值,因此为了获得最佳效果,我们还有一定的余地来应对粘度)。
在较旧的方法中,如果颜色的颜色密度过高,我们可以用清漆和/或使用不同的网纹辊将其降低。 如有疑问,可使用杯子检查粘度,这通常需要对相关传感器进行重新校准。
因为我们现在对墨水的初始温度补偿粘度有了更可靠的度量,所以可以通过将墨水稀释到正确的值来立即自动调整其粘度。 由于保持了正确的粘度值,因此可以更好地将油墨从网纹传墨辊转移到印版,最后转移到基材上。 也可以更早地注意到网纹辊的污染,因为我们知道在一定的粘度下应该达到哪种颜色强度。
粘度太高会导致转印不良,从而导致视觉特性(如不透明性和“重影”)。 由于具有更精确的粘度,因此可以更好地排空网纹传墨辊的孔,并且墨水通常流动性更好,从而使墨水层更平滑并提高了色强度。 随着速度的增加,墨水的传输减少,但是由于墨水具有正确的粘度并具有最佳性能,因此与我们使用杯校准传感器的早期方法相比,这些变化较小。
在过去六个月中,我们取得了进步 颜色 质量,并且能够保持dE2000值的偏差更小。 严格控制粘度的结果是,印刷检查系统看到的色彩强度偏差误差要少得多。 我们的操作员对传感器和控制系统的准确和可重复的值完全有信心。 这种信任使我们的印刷机无论大小,都能获得出色的印刷质量。 此外,我们没有对传感器进行维护或校准,并且超出了我们对每种墨水的初始温度补偿粘度参数的测量范围,因此无需对粘度值进行进一步的标准化。 现在我们知道特定基材应保持何种粘度。 在打印每个新订单后,我们存储粘度设置值,并将其用于同一作业的重复订单。
5%的偏差适用于一种颜色而不适用于另一种颜色,我认为最好声明我们可以在打印订单期间更好地保持dE值并将该值保持在较小的带宽范围内初始值。
那么,为什么不转换为杯秒呢?
尽管存在将粘度值从mPaS转换为DIN杯秒的公式,但我们发现放弃杯秒有几个优点。
最重要的是,它改变了我们对粘度的思考方式。 只要以杯秒为单位考虑,严格控制粘度似乎是不可能完成的任务。 我们的期望受到我们以前经验的限制,因此我们将标准设置为低于达到我们可以达到的打印质量所必需的标准。
此外,以杯秒为单位的思考使我们想要拿起一个杯子并检查这些新传感器的准确性,我们当时还不熟悉它们。 但是,使用一种几乎不可重复的方法来检查传感器的准确性可能会给人一种错误的印象,即传感器本身是不可重复的! 只有当我们将使用新传感器系统的实际打印结果与我们习惯的打印结果进行比较时,我们才能看到在陌生的新单元中进行思考的真正价值。 它使我们能够“认为很小”,从而能够看到粘度的微小变化,而这些变化本来是看不见的。 此外,它使我们能够更严格地控制粘度,这对最终产品的质量产生了直接的积极影响,这毕竟是我们的主要目标。
随着打印速度的提高和利润空间的缩小,“一次就把事情做好”变得更加重要。 初始粘度设置错误可能会导致立即产生数千米的废物。 随着 Rheonics SRV 系统使我们能够简化印刷流程,同时提高色彩质量并减少浪费。
在本系列的下一篇文章中
在本文中,我们重点关注粘度监测的基本挑战oring 和控制,展示了严格控制印刷质量和油墨经济性的好处。 在下一篇文章中,我们将更仔细地研究控制系统,该系统使印刷机操作员能够以最少的干预实现并保持这种质量。 系统, Rheonics 打印解决方案 (RPS) 由一个控制箱组成,其中包含过程计算机和阀门控制器,可根据测量的粘度直接控制溶剂稀释。 RPS 最多可容纳 10 个印刷站,并由 SRV 传感器进行监控oring。 RPS 硬件由复杂的软件系统支持,该软件系统根据测量的粘度估计所需的稀释度,并通过简单直观的用户界面进行控制,以设置和调整所需的粘度。
我们还将考虑控制特殊油墨的粘度的挑战,例如粘度对温度非常敏感且最好通过热控制来控制粘度的UV油墨。